Carpet Brush Drilling And Tufting
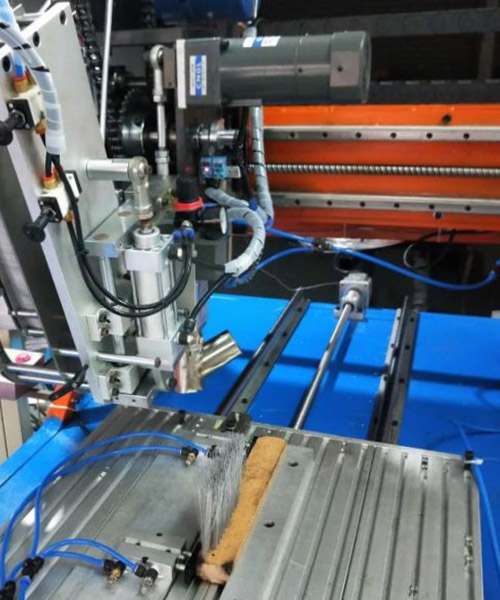
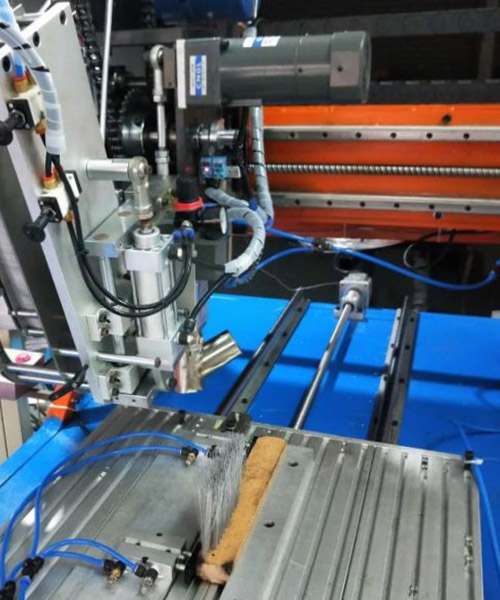
Specification
A carpet brush drilling and tufting machine is a specialized piece of equipment used for manufacturing carpet brushes, which are designed for cleaning and maintaining carpets. These machines are designed to automate the process of creating the brush tufts and, in some cases, drilling holes in the brush base for various applications.
Here is a description of the key features and components of such a machine:
Bristle Feeding System: The machine is equipped with a bristle feeding system that supplies individual bristles or bundles of bristles, typically made from durable materials suited for carpet cleaning.
Brush Base Handling: These machines may have mechanisms for handling and loading brush bases or handles, which can be made of various materials like wood, plastic, or metal. The bases provide the structure and support for the bristle tufts.
Tufting Head: The tufting head is a core component of the machine responsible for creating the brush tufts. It typically features multiple tufting needles or pins that are precisely arranged to grip and hold the bristles in a specific pattern.
Control Panel: The machine features a control panel with an interface that allows operators to set various parameters, such as tufting pattern, tufting density, speed, and other customization options.
Drilling Mechanism: Some carpet brush tufting machines are equipped with a drilling mechanism. This system is used to create holes in the brush base at precise locations, which can be beneficial for specific applications like attaching additional cleaning components or adjusting brush stiffness.
5-Axis Movement Control: The machine may feature multi-axis movement control, typically X, Y, Z, and rotational axes, allowing for precise positioning and movement of the tufting head to create complex tufting patterns or accommodate drilled holes in the brush base.
Clamping System: A clamping system secures the base of the bristles and the brush base, ensuring that the bristles are evenly spaced and firmly attached to the base.
Cutting Mechanism: Some machines may include a cutting mechanism to trim the bristles to a uniform length after tufting, ensuring a consistent brush quality.
Frame and Chassis: The machine is usually built on a sturdy frame or chassis to provide stability during operation.
Safety Features: Safety features, including emergency stop buttons, safety guards, and sensors, are integrated into the machine to protect operators and ensure safe operation.
Customization Options: The carpet brush drilling and tufting machine can be customized to create different brush designs, sizes, and patterns to meet specific carpet cleaning requirements.
These machines are essential for efficiently producing carpet brushes used in residential, commercial, and industrial settings. They automate the manufacturing process, reduce labor costs, and ensure precision in brush tufting and, where applicable, hole drilling for specialized carpet cleaning applications.