Plastic Injection Mould


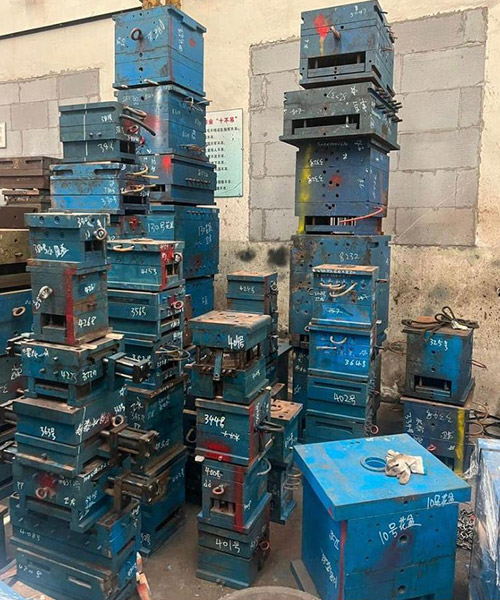
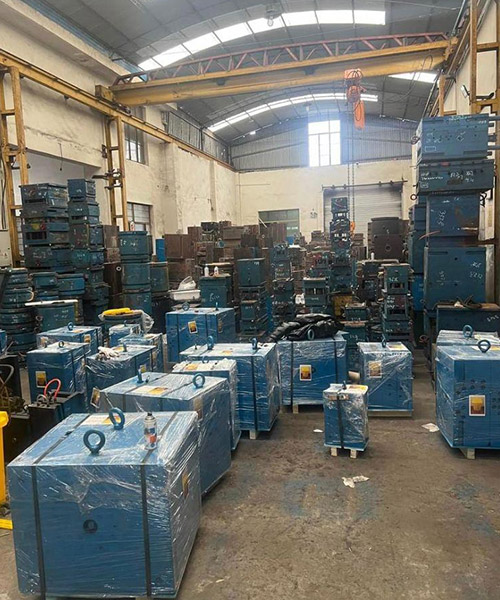


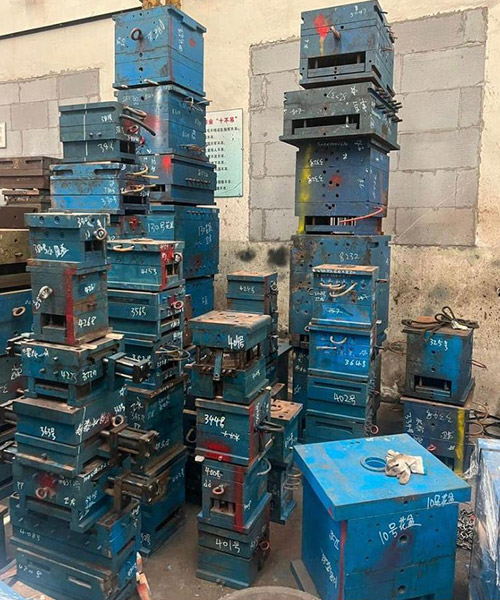
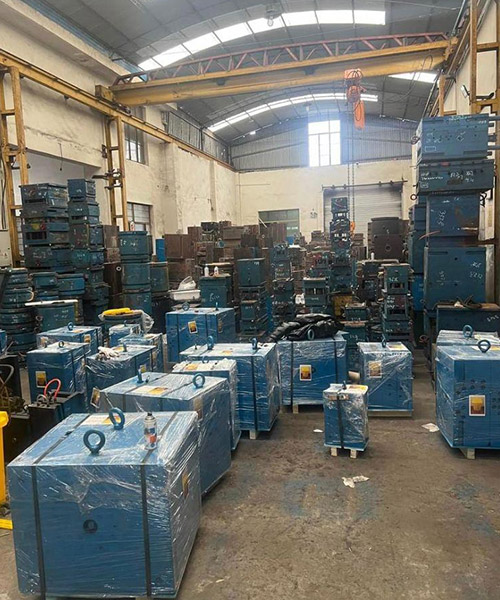
Plastic Injection Mould
A plastic injection mold, also known as an injection molding tool or die, is a specialized tool used in the plastic manufacturing process to produce plastic components and products. It plays a crucial role in shaping molten plastic material into the desired form.
Here’s a description of the key components and how plastic injection molding works:
Key Components:
Cavity and Core: The mold typically consists of two main parts, the cavity and the core. The cavity is the hollow area that shapes the exterior of the plastic part, while the core shapes the interior.
Runner System: The runner system is a network of channels or passages that allow molten plastic to flow from the injection molding machine’s nozzle into the cavity. It includes sprues, gates, and runners.
Ejector Pins: Ejector pins are used to push the finished part out of the mold once it has cooled and solidified. They are typically located on the side opposite the gate.
Cooling System: To expedite the cooling process, molds are equipped with a water cooling system. Water is circulated through channels to remove heat and maintain uniform temperature across the mold.
Injection Mold Base: The mold base provides the structural foundation for the mold’s components. It is mounted to the injection molding machine.
Working Process:
Clamping: The mold closes, and the two halves—the cavity and core—come together under high pressure. This clamping action ensures that the mold remains closed during the injection and cooling phases.
Injection: Molten plastic material is injected into the mold through the nozzle of the injection molding machine. It flows through the runner system and into the cavity.
Cooling: Once the plastic is in the mold, the cooling system circulates coolant through channels to rapidly cool and solidify the plastic. The cooling time depends on the size and thickness of the plastic part.
Ejection: After cooling, the mold opens, and ejector pins push the finished plastic part out of the mold cavity. The part is then collected or removed for further processing.
Applications:
Plastic injection molds are used in various industries to produce a wide range of plastic products and components, including:
Consumer Goods: Plastic containers, house hold brush , household appliances, and toilet brush cleaning brush and more.
Automotive: Interior and exterior components, such as dashboards, bumpers, and trim.
Medical Devices: Medical equipment and devices like syringes, IV components, and diagnostic equipment.
Plastic injection molding is a highly versatile and efficient manufacturing process for producing plastic parts in large quantities. The design and quality of the mold are critical factors in achieving precise and consistent results. The molds are typically made from durable materials, such as steel or aluminum, to withstand the high pressures and temperatures of the injection molding process.